We’re beginning with enterprise in the present day in 3D Printing Information Briefs, with tales from Nexa3D and Headmade Supplies, Desktop Metallic and FreeFORM Applied sciences, and 3D Methods. ELEGOO debuted a brand new printer at a commerce present, Intermed Labs is working to make prosthetics extra accessible, and a 3D printed microdevice may remodel male infertility therapy. Lastly, there’s some attention-grabbing analysis about assembling matter in 3D, after which bioprinting dwelling mind cell networks.
Nexa3D Enters Metallic AM House with Headmade Supplies’ ColdMetalFusion
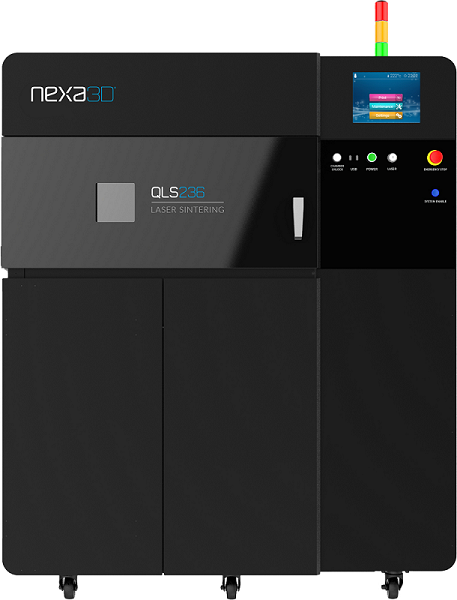
Offering ultrafast print velocity and a 24-hour cycle time, the QLS 3D printers are essentially the most versatile SLS printers available on the market, producing each polymer and metallic elements utilizing the ColdMetalFusion course of
Ultrafast polymer 3D printing supplier Nexa3D is extending its metallic SLS capabilities by way of a strategic collaboration with Headmade Supplies and its sinter-based ColdMetalFusion course of. This can make Headmade’s distinctive feedstock know-how suitable with its personal high-throughput QLS 3D printer lineup, and permit clients to get round productiveness obstacles in metallic components manufacturing. ColdMetalFusion combines established powder metallurgy processes with the benefits of polymer laser sintering, and Nexa3D will leverage the ecosystem round this course of, in order that each firms can supply gear, supplies, providers, software program, and experience to clients within the metallic manufacturing trade.
Christian Fischer, Co-CEO of Headmade Supplies, stated, “We’re impressed by the velocity and throughput capabilities of Nexa3D know-how and couldn’t be extra excited to companion with them to broaden entry and adoption of ColdMetal Fusion know-how.”
Desktop Metallic Sells Metallic Binder Jet Methods to FreeFORM Applied sciences
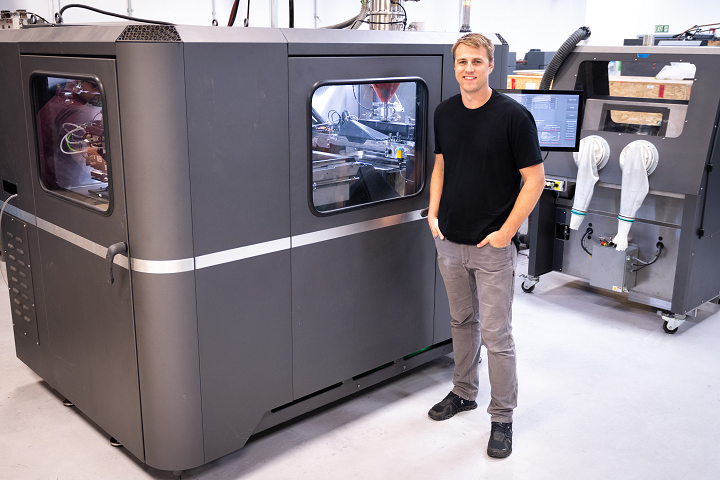
FreeFORM Applied sciences President Nate Higgins, proven in entrance of a Desktop Metallic X25Pro, now operates the world’s largest fleet of 25 Desktop Metallic binder jet 3D printers, which remodel metallic powder into complicated end-use components. The Pennsylvania-based FreeFORM can also be slated to take supply of a Manufacturing System P-50, the world’s quickest metallic binder jet system with Single Move Jetting (SPJ) know-how.
Desktop Metallic has offered a Manufacturing System P-50, and a Tremendous Fleet of metallic binder jet programs, to Pennsylvania-based FreeFORM Applied sciences, which was based in 2020 and boasts industrial metals processor and distributor Ryerson Holding Company as a number one investor. With this buy, FreeFORM now owns and operates the world’s largest fleet of Desktop Metallic printers—a complete of 25, together with the Manufacturing System, Store System, and X-Collection fashions. The corporate has produced over 350,000 components with binder jetting for world clients within the client items, protection, industrial, medical, and robotic markets.
“FreeFORM’s funding in metallic binder jetting demonstrates our continued dedication to using world-class additive manufacturing processes to fulfill the wants of our clients. This addition of DM printers strengthens our capabilities on this space, permitting us to offer larger value effectivity and velocity to market,” stated Nate Higgins, President of FreeFORM Applied sciences.
3D Methods Completes Insourcing of Manufacturing for Printer Platforms
3D Methods has accomplished a strategic initiative to streamline manufacturing by insourcing the manufacturing of two extra strategic 3D printer platforms. The exercise was transferred from two electronics manufacturing providers (EMS) companions, which the corporate maintains business relationships with to broaden world adoption of the metallic and polymer manufacturing AM platforms. The corporate now controls the entire manufacturing course of from begin to end. By insourcing these printers in Riom, France and Rock Hill, South Carolina amenities, 3D Methods can supply improved high quality management, quicker introductions of latest merchandise, and decreased manufacturing cycle instances, all of which reinforces buyer satisfaction.
“Our clients need dependable, high-quality merchandise that meet their evolving wants to be used in manufacturing facility manufacturing environments. In-house manufacturing not solely permits us to streamline manufacturing and scale back lead instances, however it additionally permits us to supply aggressive pricing by way of extra environment friendly operations,” defined Dr. Joe Zuiker, 3D Methods’ Government Vice President of Engineering & Operations. “This implies our clients can obtain larger worth from our manufacturing printers, quicker than ever earlier than. We elevate our dedication to buyer satisfaction by additionally offering printing course of options tailor-made to our clients’ distinctive necessities and distinctive buyer help. Our steady enchancment helps our clients speed up their adoption of additive manufacturing and thereby attain a aggressive benefit of their market.”
ELEGOO Debuted First Giant FDM Industrial Printer at TCT Asia
In the course of the current TCT Asia 2023 exhibition in Shanghai, ELEGOO made its profitable debut with a showcase of its newest merchandise, together with the OrangeStorm Giga, the corporate’s first giant FDM industrial 3D printer, and its Jupiter SE resin printer. ELEGOO is a fast-developing model within the world sensible manufacturing trade, specializing in R&D, gross sales, and manufacturing of consumer-grade 3D printers and sensible know-how merchandise.
At this yr’s annual occasion, ELEGOO divided its exhibition into three separate zones to supply attendees an immersive expertise {of professional} 3D printing. Within the Product Show Zone, the corporate featured its traditional consumer-grade resin and FDM printers, together with the award-winning Mars and Saturn sequence. The standout was its new light-weight OrangeStorm Giga, that includes an 800 x 800 x 1000 mm print space, Klipper high-speed silent motherboard, distinctive extrusion design, and fast setup. The Printing Zone allowed guests to immerse themselves in 3D printing, with product engineers readily available to reply questions and supply steerage. Lastly, ELEGOO additionally arrange a zone for mannequin showcasing, targeted on widespread trade functions like jewellery design, instructional fashions, and anime collectible figurines.
Intermed Labs Makes 3D Printed Prosthetics Accessible
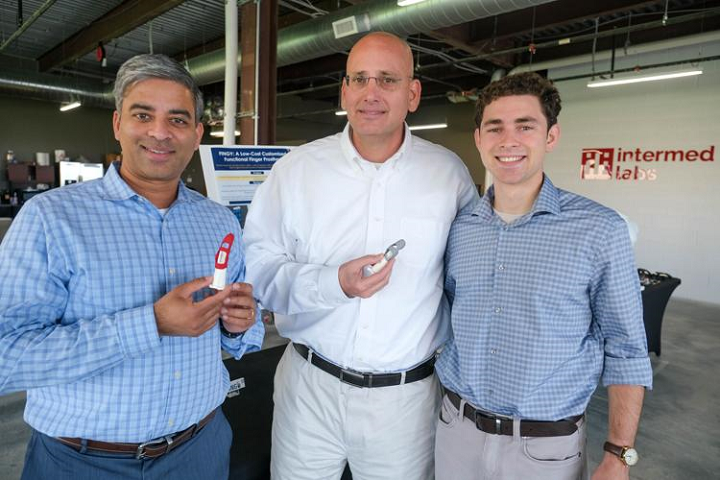
Ashok Aggarwal, Tom McClellan and Ryan Gross inside their enterprise startup studio, Intermed Labs, in Morgantown, the place they designed Fingy3D, a approach to cheaply manufacture finger prosthetics utilizing AI and 3D printers. Regardless of an preliminary curiosity in working for NASA or SpaceX, Intermed impressed Gross sufficient with the standard of its initiatives that he selected to work on the startup studio as an alternative. “We now have unimaginable expertise within the state,” McClellan stated. “And I’m actually pleased with the truth that had been using a few of that expertise. We’re going to make this space of West Virginia a tech hub. I’m gonna hold saying till it occurs.” Picture by Esteban Fernandez
Plastic and reconstructive surgeon Dr. Tom McClellan is the CEO of enterprise startup studio Intermed Labs, based mostly in Morgantown, West Virginia. The corporate helps advance technological breakthroughs, and create actual, workable units which can be delivered to market, which docs give you to enhance affected person care—like Fingy3D. These 3D printed on-demand prosthetic fingers are very accessible—sufferers take a mobile phone image of their hand from wherever on this planet, ship it to the corporate, and AI views the {photograph} and sculpts a drawing of the prosthetic, which is then put right into a CAD program to create a 3D printable file. Plus, Fingy3D prosthetics begin at $300, versus the everyday $5,000 price ticket that may be a barrier to many sufferers. The Intermed Labs group hopes Fingy3D will ultimately be bought by an organization that has the sources to convey it to extra individuals across the globe.
“You understand, prosthetics are wanted in different international locations, perhaps much more so than the U.S. Having a corporation that has broader attain, I feel may positively permit this to scale,” stated Ashok Aggarwal, Technique and Know-how, Intermed Labs. “In all probability scale back the fee that this product has, which is already so low, however it’s doable that it may be lowered even additional and actually simply get within the fingers of increasingly more individuals which can be dwelling not less than some a part of their life sub-optimally.”
3D Printed Microdevice May Enhance Success of Male Infertility Therapy
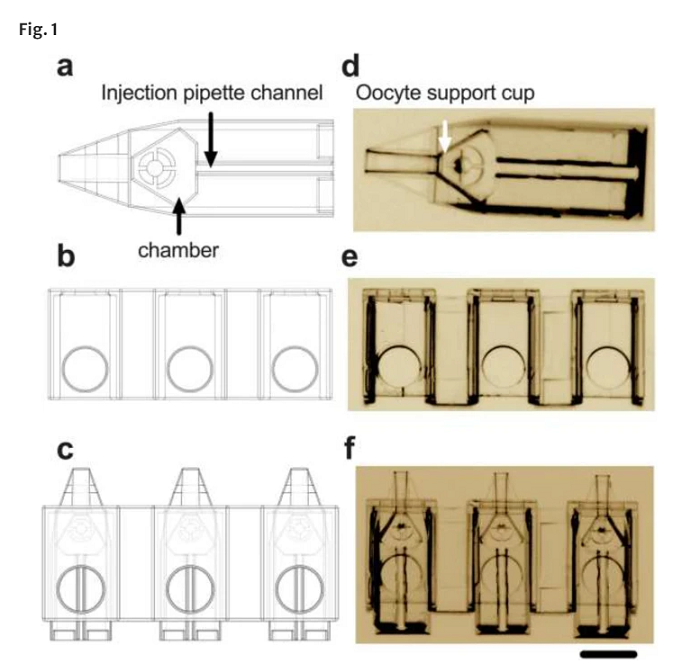
Design and fabrication of a tool on the micron scale for oocyte microinjection. Three-dimensional schematic of the Pod (a) and Storage (b) and an illustration of three Pods docked inside a Storage (c). The Pod (d) and Storage (e) had been fabricated utilizing two-photon polymerization (Nanoscribe GmBH, Eggenstein-Leopoldshafen, Germany). In (c) and (f), 3 Pods are docked inside a Storage (1500 × 450 × 310 μm; l × w × h). The Pod (725 × 250 × 250 μm) contains entry for an injection pipette (injection pipette channel (a and d)) and a chamber with a raised mattress that homes and holds the oocyte throughout microinjection (oocyte help cup (a and d)). Photographs (d, e, and f) had been taken utilizing a 20 × goal with a last magnification of 20 × (Nikon SMZ1500 microscope, Nikon Devices, Inc., NY, USA). Scale bar = 250 μm
A group of researchers from the College of Adelaide wish to enhance in vitro fertilisation (IVF) with a 3D printed microdevice that streamlines the intracytoplasmic sperm injection (ICSI) process—the one accessible therapy for males with low sperm counts. Presently, eggs and sperm are picked up with tiny suction units, that are then aligned in a 3D area for injection. However this requires extraordinarily delicate fingers, or irreversible injury could be brought on. It’s now doable to 3D print units which can be sufficiently small to carry particular person eggs for the process, and this microdevice is smaller than a pinhead. It comprises pods that home single eggs, that are picked up with wonderful forceps and docked in a supporting gadget, so the embryologist is aware of precisely the place they’re. The gadget, which already went by way of preclinical trials, streamlines the method, and is within the means of being commercialized by medtech firm Fertilis.
“With this new course of, an embryologist … can turn out to be extremely expert at ICSI, and hopefully we gained’t see the variability in success throughout totally different clinics and totally different embryologists,” stated lead researcher Dr Kylie Dunning from the Robinson Analysis Institute. “Hopefully it may be a one-stop store, the place embryologists can carry out the injection and embryo tradition within the one gadget.”
You possibly can study extra within the group’s analysis paper.
Optimized Acoustic Holograms for 3D Printing Organic Cells
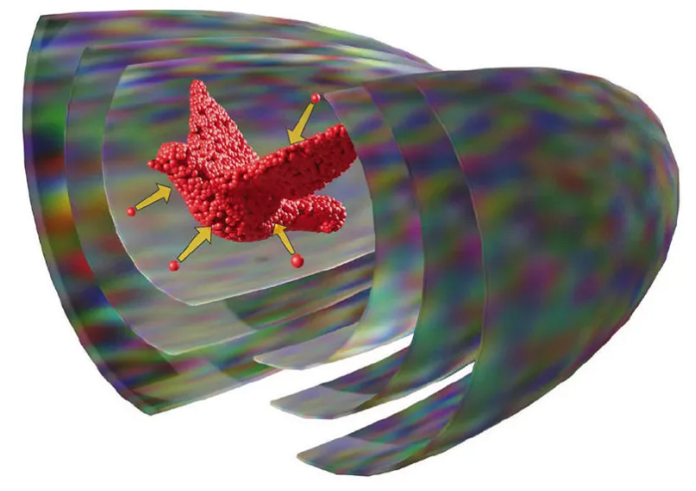
Using sound waves to create a strain discipline to print particles. (Picture: MPI for Medical Analysis, Heidelberg College/Kai Melde)
Persevering with with analysis, a group from Heidelberg College and Max Planck Institute for Medical Analysis developed a methodology for assembling matter in 3D, and it makes use of sound waves. In typical 3D printing, objects are constructed a layer at a time, however these researchers found out how one can kind a 3D object from smaller constructing blocks in a single step. The method makes use of a number of acoustic holograms—optimized with an algorithm—to generate strain fields with which gel and hydrogel beads, strong particles, and organic cells could be 3D printed. The group captured cells and particles floating freely in water, and used high-frequency ultrasound to push the wavelengths into the microscopic realms and manipulate them into 3D shapes. Ultrasound is light on organic cells, and may journey deep into tissue for distant formulation, so this work may result in novel 3D cell tradition methods for biomedical engineering.
“The essential concept was to make use of a number of acoustic holograms collectively and kind a mixed discipline that may catch the particles,” defined Kai Melde, postdoc within the group and first writer of the examine.
3D Printing Nerve Networks within the Lab with Bioinks
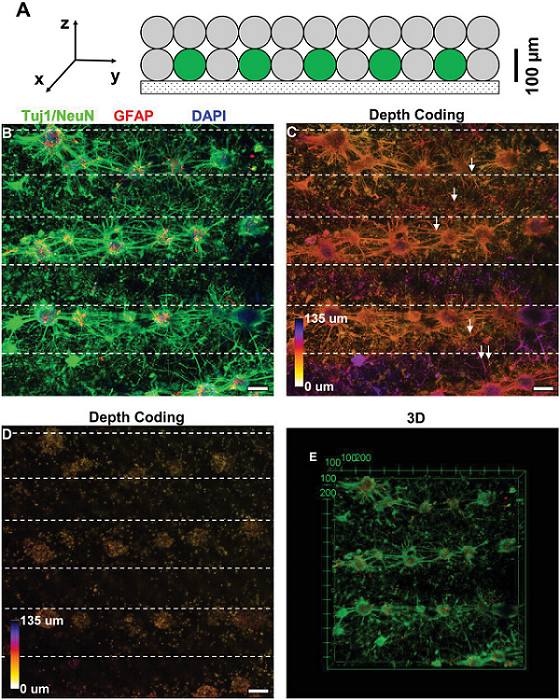
Bioprinted cortical neurons and astrocytes after in vitro tradition at 7DIV. A) Cross-section view of bioprinted construction consisting of mobile (inexperienced) and acellular (gray) strands. B) Most depth projection of patterned construction: mobile–acellular–mobile. Neurons (NeuN, inexperienced), astrocytes (GFAP, purple), and nuclei (DAPI, blue) had been colocalized and developed complicated constructions. Axons (Tuj1, inexperienced) originating from the proximal mobile strands projected throughout the distal mobile strand. C) Depth-coding of Tuj1/NeuN confirmed the event of axonal projections throughout strands. White arrows point out neurites that belong to totally different focal planes. D) Depth-coding of DAPI reveals localization of cell nuclei. E) Confocal picture in 3D. Depth-coding was represented utilizing a colour bar: purple, closest to the glass substrate, and blue, 135 µm away from the substrate. Scale bar, 100 µm.
Lastly, researchers from Monash College have 3D printed bioinks containing dwelling nerve cells (neurons) that may develop within the lab, and really transmit and reply to nerve alerts. 2D nerve cell cultures have been used previously to check how nerve networks and illness mechanisms are shaped, however the flatter constructions don’t actually mirror how the neurons develop and work together with their environment. Alternatively, bioprinted 3D neural networks have potential for deep examine of the formation and progress of nerves and nerve networks, screening medication for his or her results on the nervous system, and investigating how some illnesses can have an effect on neurotransmission. The group used tissue engineering and bioprinting to imitate the association of white and gray matter within the mind, and delicate electrophysiological measurements confirmed that spontaneous nerve-like exercise was taking place within the dwelling mind cell networks, together with responses ensuing from drug and electrical stimulation.
“The networks grown on this analysis carefully replicated the 3D nature of circuits in a dwelling mind, the place nerve cells prolong processes referred to as neurites to kind connections between totally different layers of the cortex,” stated Professor John Forsythe of the Division of Supplies Science and Engineering, who’s main the analysis.
“We discovered that the projections rising from neurons within the printed ‘gray matter’ or mobile layer readily grew by way of the ‘white matter’ layer and used it as a ‘freeway’ to speak with neurons in different layers.
“Not solely had been we in a position to assemble a fundamental structure much like what we see in areas of the mind, we discovered that the neurons really behaved and carried out in an analogous method.”
You possibly can study extra within the group’s examine.
Subscribe to Our Electronic mail Publication
Keep up-to-date on all the newest information from the 3D printing trade and obtain data and provides from third social gathering distributors.